Pressure vessels such as pipelines, plumbing, gas cylinders, boilers, above-ground storage tanks (ASTs), and fuel tanks are typically required to undergo hydrostatic testing for strength and leaks. Testing pressure vessels to transport and store gases is vital because such containers can explode if they fail under pressure. Hydrostatic testing is a well-known industry standard test involving filling the vessel or pipe system with a liquid, usually water, and pressuring the vessel to the specified test pressure. Pressure loss would indicate a leak. A dye may be used for visual identification of the leak location.
These pressure vessels are most commonly constructed from carbon steel alloys that are generally prone to electrochemical corrosion during hydrostatic testing and during transport and/or storage if not effectively dried and/or protected using supplemental corrosion inhibitors or inert gas purging. The hydro-test water used supplies the electrolyte required for the electrochemical corrosion cell. The quality of the water used for hydrostatic testing varies from high-quality deionized water to highly corrosive sea or brackish water. The type of water used directly influences the rate that electrochemical corrosion initiates and propagates. Chemical additives, i.e., contact and/or vapor corrosion inhibitors (VCI), oxygen scavengers, or a combination of all three may be added to the water to prevent or arrest corrosion.
In managing hydro-test waters, pollution prevention and control measures should be implemented. This can be accomplished by:
- Using the same hydro-test water for multiple tests to conserve water and minimize discharges of potentially contaminated effluent;
- Reducing the concentration of corrosion inhibiting or other chemicals by using high-quality water such as deionized or reverse osmosis water;
- Selecting the least hazardous alternative with regards to toxicity, operator safety, biodegradability, and bioaccumulation potential;
- Dosing according to local regulatory requirements and manufacturer recommendations.
- Suppose discharge of hydro-test waters to the sea, surface water, or soil is the only feasible alternative for disposal. In that case, a hydro-test water disposal plan should be prepared considering location and rate of discharge, chemical use (if any), dispersion, environmental risk, and required monitoring.
Both oxygen and water are required for rust to form. Even over several weeks, ferrous metals immersed in deoxygenated water will not rust. Mechanical deaeration and chemical deoxygenation, i.e., oxygen scavengers, effectively counter corrosion while the treated electrolyte is in contact with the metal substrate. Mechanical deaerators work by heating the water and venting the gases. This operation reduces oxygen in the makeup by more than 99%, leaving oxygen concentrations measured in the parts-per-billion range. However, at feedwater and boiler water temperatures, for example, even this level can create severe corrosion. Therefore, the last traces of oxygen must be chemically scavenged from the feedwater using chemical oxygen scavengers dosed into the water, usually in parts per million concentrations. Proper mechanical deaeration is necessary for a well-run, cost-effective oxygen scavenging water treatment program. Mechanical deaeration is costly!
The disadvantage and limitations of using deaeration/deoxygenation to control corrosion result from the distinct potential for flash corrosion to spontaneously initiate when the tested vessels are emptied of their treated hydro-test water and exposed to atmospheric oxygen. When oxygen has access to a damp metal substrate, the corrosion process is hastened. However, it is promoted most in areas with the lowest oxygen concentration. If the area of the electrolyte adjacent to the metal shows low metal ion concentration, the region will turn anodic to the rest of the metal surface. Consequently, these areas will corrode quickly to boost the local concentration of ions. Another often overlooked corrosion risk associated with using oxygen scavengers is their incompatibility with biocides. This is a significant problem in the oil and gas industry. For example, decisions are often required on whether microbial-induced corrosion control takes precedence over electrochemical corrosion control or vice versa. However, this requires a separate discussion.
The use of contact corrosion inhibitors for hydrostatic testing instead of deaeration/deoxygenation methods is favored by many fabricators and has many distinct advantages. The chemistries used as contact corrosion inhibitors are typically organic or inorganic and range widely relative to safety, efficacy, and toxicity. In addition, using highly effective, non-toxic, safe, and environmentally compliant contact corrosion inhibitors is highly desirous given the large volumes of hydro-test water used for these tests when large vessels such as boilers or pipelines are tested, for example.
![]() 170,000 liter boiler |
![]()
|
The treated hydro-test water will have to be disposed of at some point. The fate of that hydro-test water will be determined by what chemicals are contained within it. Waste treating it onsite or hauling it away for waste treatment is not desirous and very expensive. What if it could be safely discharged to a municipal sewer or broadcast spread over soil to suppress dust at construction sites or used to water plants or crops without harming the environment or animals and humans?
ZERUST® AxxaVis™ HST-10 is an effective, safe, non-toxic, and environmentally compliant hydrostatic test corrosion inhibitor additive made from food-grade additives. Use concentrations are determined based on water hardness and chloride content. AxxaVis™ HST-10 offers excellent contact corrosion inhibition to all ferrous metals during hydrostatic testing operations, as well as superior flash corrosion inhibition following the draining of the hydro-test solution and drying of the vessel interior surfaces.
![]() Steel drum interior: One (1) year after being treated with a 0.5% solution of AxxaVis™ HST-10 |
![]() 1010 steel panels immersed for 7 months in 60 ppm chloride water. Left panel: with 0.5% HST-10; Right panel: control. |
A large OEM suffered severe corrosion problems of their units due to their incumbent hydrostatic test operation. Photos below show the corroded header plate inside a typical unit immediately after draining the hydro-test water.
![]() |
![]() |
Immediately after hydrostatic testing – Advanced corrosion of header plate |
AxxaVis™ HST-10 was added to the hydro-test water. The photo below shows a test unit one (1) week after hydrostatic testing.
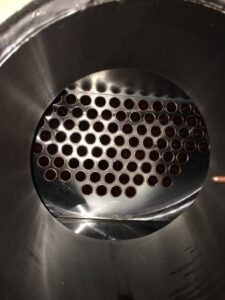
A manufacturer of heat recovery steam generator harp assemblies suffered corrosion of internal pipe surfaces during and after hydrostatic testing due to the corrosive nature of the hydro-test water. Adding 1% HST-10 to the test water resolved this problem.
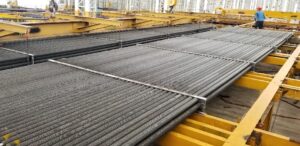
![]() Without HST-10: Note the brownish color of the water |
![]() With HST-10: Hydro-test water remains water white |
As determined by an independent 3rd party laboratory soil-spike test, it is possible to broadcast and distribute a used, clean solution of AxxaVis™ HST-10 that is free of oils and soluble contaminants over the soil. In addition, discarding used, clean HST-10 solutions into municipal drains is also possible. However, in both cases, the local authorities hold jurisdiction over handling waste streams and must be consulted before discharging any HST-10 solutions.
Conclusion:
In managing hydro-test waters, pollution prevention and control measures should be implemented. AxxaVis™ HST-10 offers the following advantages:
- Using the same hydro-test water for multiple tests to conserve water and minimize discharges of potentially contaminated effluent;
- The AxxaVis™ HST-10 solution can be easily analyzed and replenished for extended use
- Reducing the concentration of corrosion inhibiting or other chemicals by using high-quality water such as deionized or reverse osmosis water;
- It is highly recommended to use high-quality water for hydrostatic testing as this allows for lower concentrations of corrosion inhibitors. However, the AxxaVis™ HST-10 was designed to be effective even with lower quality water such as potable city water or water with high hardness and chlorides. Therefore, the use of concentration is dictated by water quality.
- Selecting the least hazardous alternative with regards to toxicity, operator safety, biodegradability, and bioaccumulation potential;
- AxxaVis™ HST-10 is made using food-grade additives that are non-toxic, operator safe, 100% biodegradable, and have zero bioaccumulation potential.
- Dosing according to local regulatory requirements and manufacturer recommendations.
- Suppose the discharge of hydro-test waters to the sea, surface water, or the soil is the only feasible alternative for disposal. In that case, a hydro-test water disposal plan should be prepared considering location and rate of discharge, chemical use (if any), dispersion, environmental risk, and required monitoring.
- “Clean” solutions of AxxaVis™ HST-10 can be discharged into municipal sewer systems or broadcast spread over the soil. It is, however, important to first consult with the local authorities. Discharge into waterways or seawater is prohibited.
AxxaVis™ HST-10 offers effective and robust contact corrosion protection during short-term and extended hydrostatic testing programs, as well as effective flash corrosion inhibition of the wet surfaces following the draining of the hydro-test water. Furthermore, treated surfaces that are dry and exposed in controlled environments of ≤ 77oF (25oC) and ≤ 55% RH are afforded short-term corrosion protection of up to 30 days or more without the use of additional corrosion inhibitors.