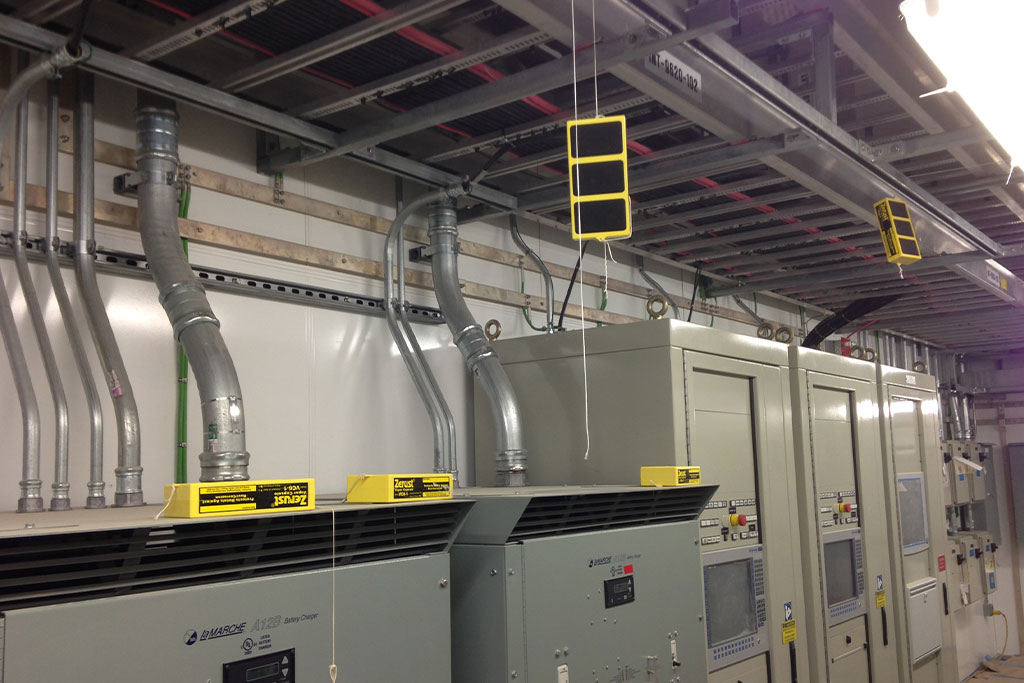
Corrosion Control for Control Rooms and Electronics: A Comprehensive Guide
Corrosion is a silent threat that plagues control rooms and electronics in industrial settings. As a result, it can cause circuitry failures, compromise equipment reliability, and ultimately lead to costly downtime. In this blog post, we’ll explore the challenges of corrosion control in control rooms and electronics and how innovative products like ZERUST® ActivDri™ Packets,
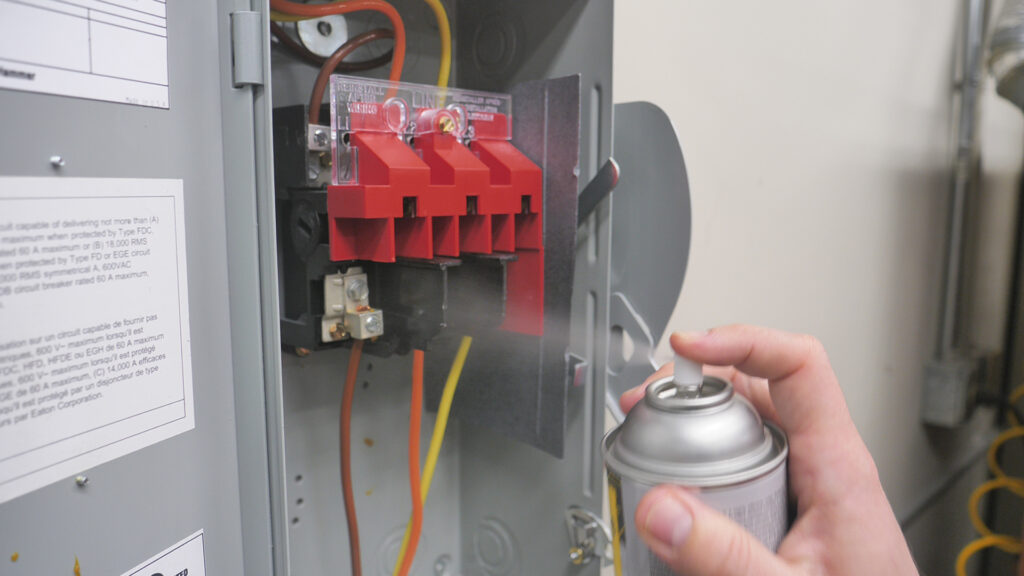
Axxanol™ 718-ESS vs. Conformal Coatings: Choosing the Right Corrosion Protection Solution
Corrosion protection holds key importance in electrical and electronic applications. Two common approaches for achieving this are conformal coatings (CC) and ZERUST® Axxanol™ 718-ESS, a multimetal electrical corrosion inhibitor spray. In this blog post, we’ll delve into the key differences between these two methods, their respective advantages and disadvantages, and how Axxanol™ 718-ESS stacks up
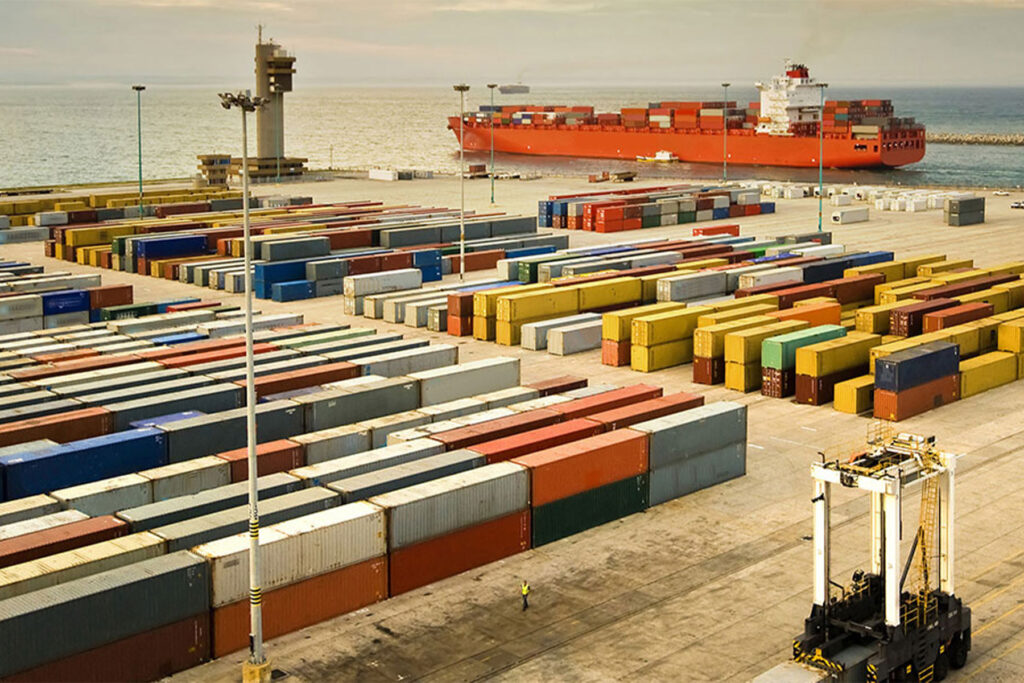
Preventing Corrosion in Metal Goods During Transit: ZERUST® Transit Coatings
Globalization is based on transporting metal goods, but it has challenges. One of these challenges is protecting metal goods from corrosion during domestic and international transit. As a result, manufacturers transporting metal goods can suffer significant financial losses and reputational damage due to corrosion. Fortunately, ZERUST® transit coatings offer a reliable solution to this problem.
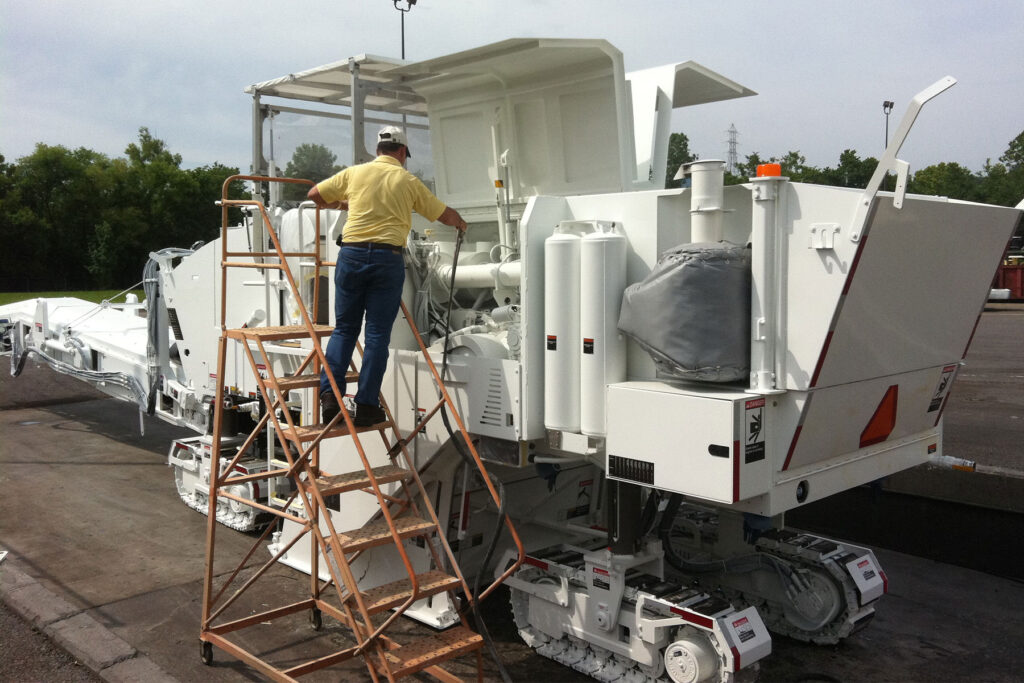
What Is the Best Rust Preventative for Your Application?
Rust is a persistent problem for metal surfaces, especially those exposed to harsh environments. If left unchecked, rust can cause significant damage and undermine the strength of metal objects. So, to safeguard against rust, it’s essential to use the right rust preventative. But with so many options available, it can be tough to determine which
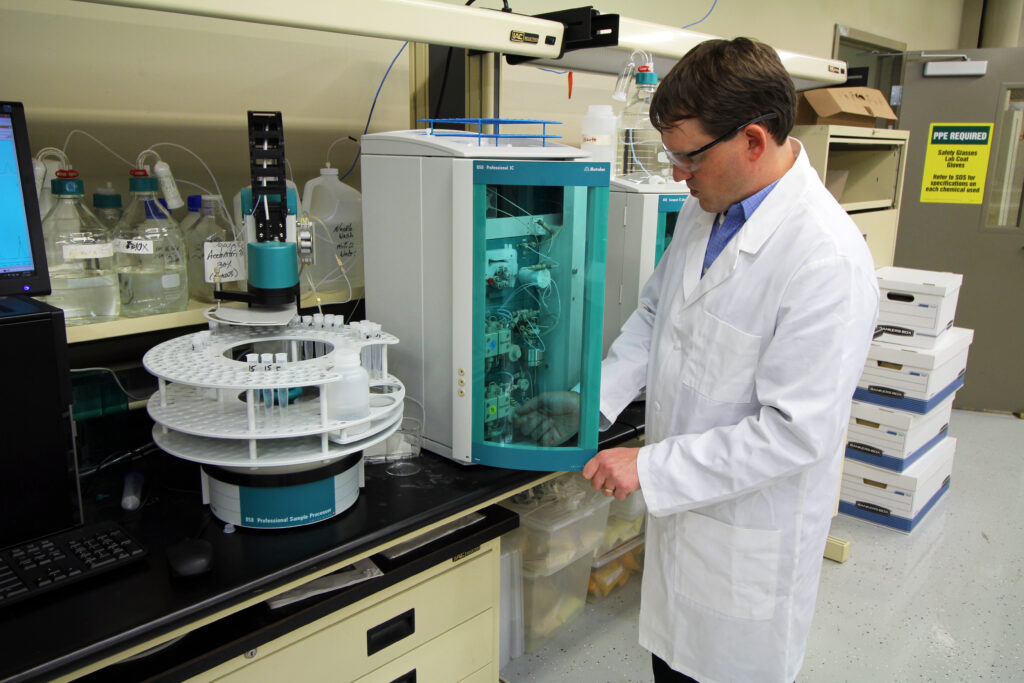
What to Do When Rust Prevention Fails?
In the manufacturing world, many companies go to great lengths to select products and processes to prevent rust and corrosion from forming on their valuable metal assets during transit and storage. They will probably incorporate volatile corrosion inhibitor (VCI) packaging, rust preventative (RP) coatings, desiccants, or some combination of them. But what happens when their
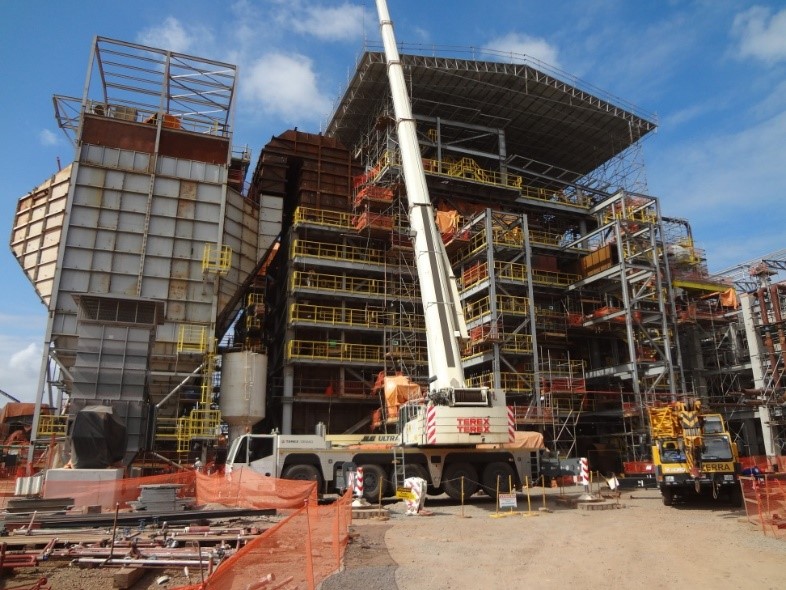
AxxaVis™ HST-10 – An Environmentally Friendly and Effective Hydrostatic Testing Additive
Pressure vessels such as pipelines, plumbing, gas cylinders, boilers, above-ground storage tanks (ASTs), and fuel tanks are typically required to undergo hydrostatic testing for strength and leaks. Testing pressure vessels to transport and store gases is vital because such containers can explode if they fail under pressure. Hydrostatic testing is a well-known industry standard test
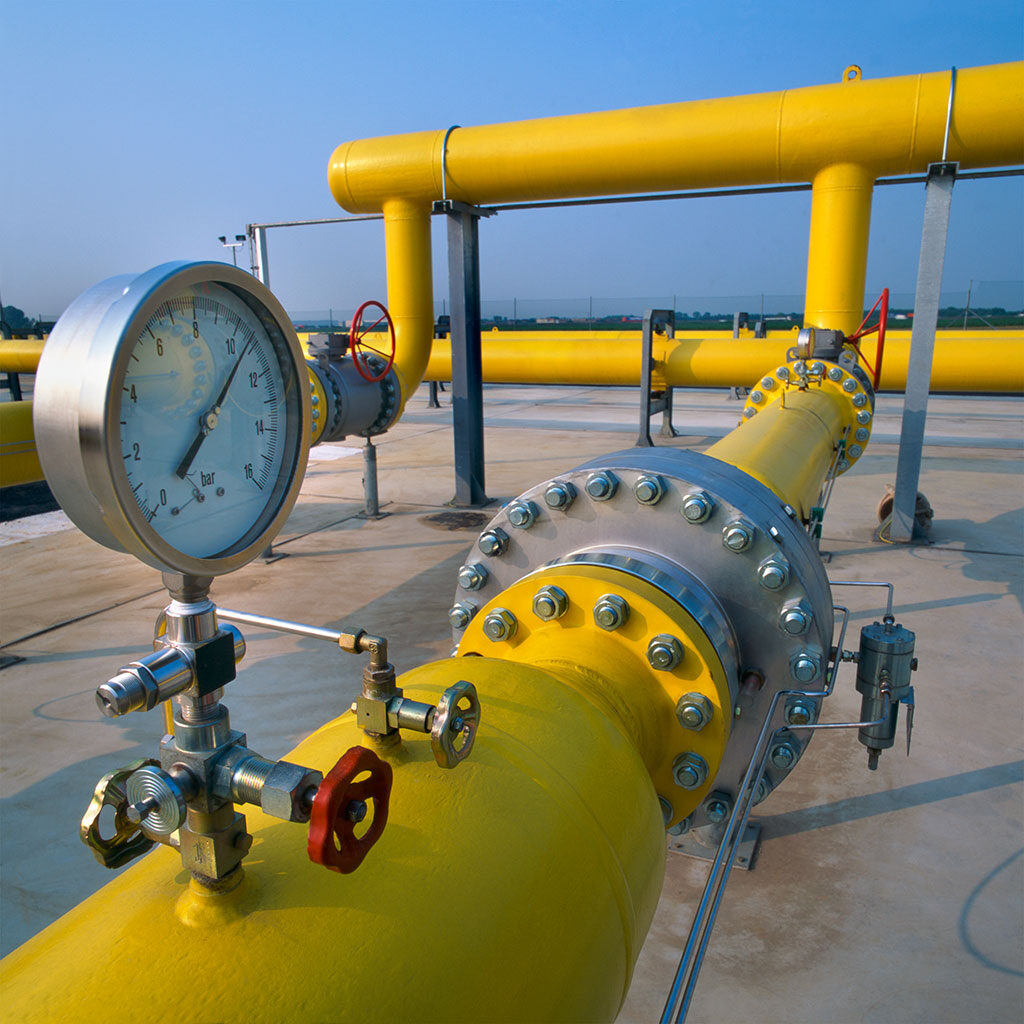
Corrosion Solutions for Hydrostatic Testing
Hydrostatic testing of pressure vessels such as pipes, heat exchangers, storage tanks, and ship voids is an essential method for quality control of parts after production and during use. This process demonstrates the fitness of the pressurized component for service after production or repair. Hydrostatic testing consists of raising the pressure level above the operating
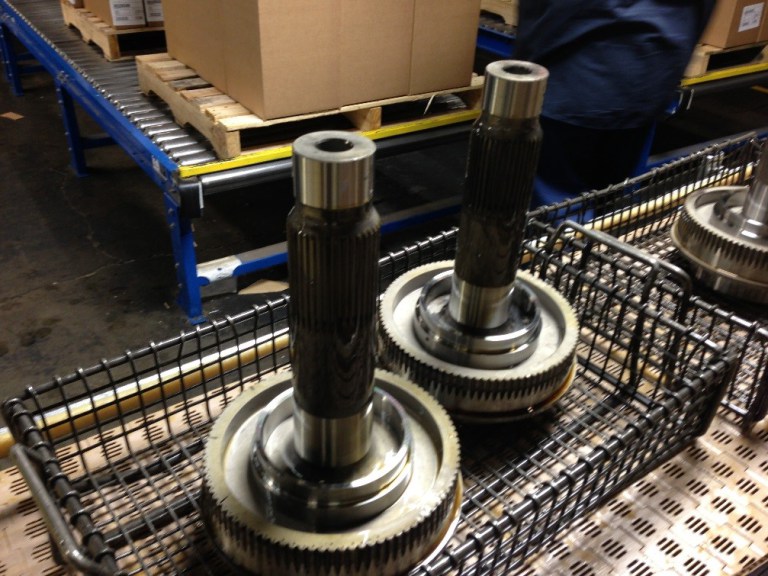
RP Oils or VCIs: Which Protection Method is Best for Me?
When considering corrosion protection methods, plenty of options are available. The two methods most used for protecting metals during the manufacturing processes of shipment and storage are corrosion inhibitor liquids and VCI (volatile corrosion inhibitor) packaging products. Corrosion inhibitor liquids, also known as “Rust Preventatives” (RPs) or oils, are available in a wide range of