Problem
Newly manufactured rotary drills bits shipping from the U.S. to Saudi Arabia and are required to have no corrosion upon arrival and inspection by the customer. Cosmoline was the current corrosion prevention product being used, and the application process involved dipping the heavy and large awkwardly sized drill bits into a tank of the Cosmoline. The operators did not like the odor and the mess that it created during the removal from the dip tank.
When their customer kept complaining about the amount of time and difficulty required with the removal of the Cosmoline’s waxy coating, the manufacture reached out to ZERUST® for a VCI solution.
Solution
The corrosion prevention solution involved the use of the ZERUST® VCI film and ActivPak® diffuser packets. This resulted in a dry-pack method, eliminating the need for the application and removal of an oily or waxy coating.
ZERUST® packaging considerations were required for the wood shipping crate and the shipping environment during the overseas journey. Wood shipping crates and 2 x 4 lumber are being used to contain, then block and brace the drill bits in place. Most wood shipping containers have a naturally occurring acetic acid makeup. Up to 7% of the woods acetic acid will release as a vapor over time. The acetic acid gases will attack metals and cause corrosion, more rapidly where the metal is in direct contact with a wood surface.
Additionally, the contained drill bits will be at sea and exposed to both salt air and higher humidity levels with the potential for container rain (see diagram).
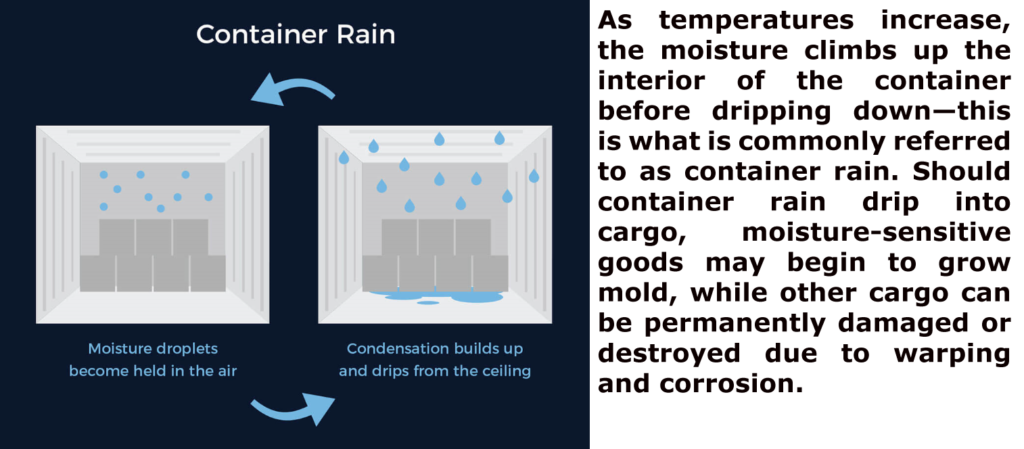
The use of ZERUST® ActivPak® diffuser packets (deployed within the ZERUST® VCI bag), will neutralize the acidity of the wood crate environment and deactivate the chlorides, that are able to migrate thru the VCI bag. The ZERUST® VCI bag serves a dual purpose in this application, the bag both contains the active ingredients of the ActivPak® and converts any moisture present in the VCI bag into a corrosion inhibitor.